INSTRUMENTAÇÃO
e regulação nas instalações fabris
da Portucel em Cacia
POR F. GONÇALVES LAVRADOR *
Quando, em 1965, comecei a exercer a minha
profissão nas instalações fabris do complexo de Cacia (e digo «complexo»
por se tratar, em boa verdade, dum conjunto de fábricas diferentes,
embora interligadas e integradas num sistema comum de gestão e
exploração), já encontrei, no campo da instrumentação e da regulação
automática, um número razoável de equipamentos e de aparelhos, com
predomínio evidente das regulações pneumáticas que, no nosso ofício,
costumamos designar por «clássicas», e com um único grande sistema do
tipo electrónico instalado na Máquina de Papel.
Nos sistemas clássicos limitados, que eram
normalmente do tipo de monolacete (controlando apenas uma variável de
processo e sem cadeias de lacetes), incluíam-se primitivos aparelhos de
medição de consistência, colunas de mercúrio, manómetros tipo bourdon e
de helicóide, células de pressão diferencial, diafragmas, foles,
termopares, sistemas termais de pressão e de expansão, orifícios de
medição de caudal, balanças, borbulhadores, controladores auto-actuantes
ou actuantes por relé ou por piloto e baseados no mecanismo
bico-palheta, válvulas de controle pneumáticas de vários tipos, etc.
Tudo aparelhagem de tipo analógico. Pouco equipamento electrónico
existia então no campo dos circuitos limitados de controle.
Quanto a sistemas globais, já nos referimos
à máquina de papel como sendo o único digno de nota, pois pouco ou nada
existia, nessa altura, nas máquinas de tiragem de pasta (com
accionamentos muito primitivos) e na própria fábrica de Embalagens de
Papel (com uma máquina de canelar cujo sistema de regulação de
velocidade era também bastante ultrapassado).
Uma máquina de tiragem de pasta ou uma
máquina de papel, nomeadamente de tipo Fourdrinier (como a de Cacia),
apresenta-se sempre como um equipamento de grandes dimensões que se
desenvolve longitudinalmente num longo percurso, com transporte do
produto, constituído por uma «folha» contínua, duma extremidade (a
extremidade húmida onde se forma a referida folha) até à outra
extremidade, onde se acumula numa bobine o produto acabado. Este tipo de
processo, cujas particularidades não podemos desenvolver aqui, impõe
delicadas exigências de regulação e de controle. Há duas possibilidades
de accionamento eléctrico duma máquina de tal tipo, a saber: a) com um
só motor (que pode ser de velocidade ajustável ou de velocidade
constante mas acoplado a um variador de velocidade de qualquer tipo
mecânico), ou seja, um accionamento eléctrico global; b) com um certo
número de motores, cada um a accionar a sua parte ou secção da máquina,
ou seja, um accionamento seccional. O primeiro tipo está há muito
obsoleto, considerando-se inaplicável nos grandes equipamentos de
tiragem das fábricas modernas. Adopta-se, portanto, o accionamento
seccional que, contudo, impõe a necessidade dum mecanismo de controle
cujo propósito principal consiste em harmonizar a rodagem de todas as
secções do equipamento. O primeiro método atrás referido apenas permite
o ajustamento da velocidade de toda a máquina dentro duma só faixa de
velocidades (do motor ou do variador de velocidade), exigindo que o
ajustamento da velocidade das secções devido a condicionamentos locais
dependa ainda de complicados e hoje pouco aceitáveis (ou mesmo
inaceitáveis) processos mecânicos de variação. O segundo método não só
torna possível uma variação uniforme da velocidade em toda a máquina,
mas também possibilita que essa variação seja finamente graduada, muito
sensível e muito eficaz na sua acção, diferenciando-se nas várias
secções quando os condicionamentos de carga e de alimentação se
alterarem de modo também diferenciado nessas mesmas secções. Mas há
mais: esta acção correctiva é executada como que instantaneamente, pelo
menos quando comparada com os processos correctivos de tipo mecânico, e
com muito menos probabilidade de avarias ou de instabilidades
funcionais. Deve acrescentar-se, por fim, que se adoptam como motores
eléctricos de accionamento os motores de corrente contínua, devido à
facilidade que oferecem para se conseguir um controle suave e contínuo
da velocidade.
Isto basta para se compreender por que razão
o accionamento da máquina de papel de Cacia é do tipo seccional,
utilizando, portanto, motores de corrente contínua individuais em cada
secção e controle electrónico que começou a ser estudado e aplicado
parcialmente pela General Electric a partir de 1937 e que se
comercializou como tipo de regulação exclusiva de toda a máquina a
partir de 1941.
Os grandes melhoramentos introduzidos no
material electrónico durante a Segunda Guerra Mundial, sobretudo o
desenvolvimento de novas válvulas de vácuo, levou à adopção pela G. E.,
a partir de 1945 e em todos os accionamentos seccionais de máquinas de
papel, do regulador electrónico de velocidade com amplidínamo. Este
sistema podia servir (mediante pequenas modificações de ligações
internas) como regulador de velocidade, regulador de tensão, regulador
de corrente ou limitador de corrente de arranque dum motor. É este
precisamente o sistema instalado na máquina de papel de Cacia e ainda
hoje a trabalhar com pleno rendimento.
A velocidade do motor da secção que se
considere é medida através da tensão dum gerador piloto de corrente
/ 34
/ contínua e de íman
permanente (taquímetro). Esta tensão é comparada com uma tensão
eléctrica de referência controlada com rigor e pré-escolhida de acordo
com a velocidade desejada. A tensão diferencial resultante, se existir,
é amplificada, primeiro electronicamente por um amplificador «clássico»
de válvulas, e depois por um amplificador rotativo chamado amplidínamo
que controla o campo do gerador que, por sua vez, fornece potência
eléctrica ao motor da secção considerada. Quando o gerador fornece
potência a diversos motores seccionais, usa-se a saída do amplidínamo
para controlar a excitação (ou campo) dos motores. Desta maneira
corrige-se rapidamente qualquer desvio da velocidade relativamente a um
valor pré-escolhido e comum a todas as secções.
Não vamos, evidentemente, entrar em
pormenores sobre o sistema de controle que acabamos de referir. A
descrição aqui feita serve apenas para salientar dois elementos
fundamentais: a utilização de grandes grupos motores-geradores para a
conversão da corrente alternada para contínua e a aplicação de
pré-amplificadores de válvulas electrónicas e de amplificadores
rotativos (amplidínamos). Daqui se conclui que a parte de potência (além
da força motriz, evidentemente) se baseia em conversores rotativos e que
a parte de controle é electrónica, ou melhor talvez, semi-electrónica,
dada a utilização duma máquina rotativa e com escovas, o amplidínamo, e
de muitas unidades de comutação de tipo electromecânico (relés e
comutadores).
Na época em que se encomendou este sistema,
no início dos anos cinquenta, estava sem sombra de dúvida actualizado.
Mas, nos anos seguintes, o desenvolvimento da electrónica de controle e
mesmo de potência foi (e continua a ser, aliás) tão vertiginoso que,
dentro dum período de tempo muito curto (e isso já acontecia em 1965),
ele estava tecnicamente ultrapassado, o que não significa de modo nenhum
que não se trate de aparelhagem de alta eficiência que satisfaz
inteiramente os seus utilizadores, e ainda continua a satisfazer nos
dias de hoje, apesar da idade e do seu inevitável envelhecimento, não
apenas devido à robustez das unidades instaladas, mas também devido aos
cuidados constantes do pessoal especializado responsável pela respectiva
conservação.
A partir de 1965, as constantes ampliações
da Central Geradora, da Fábrica de Pasta, do Branqueamento e da Fábrica
de Embalagens de Papel introduziram novos equipamentos de medição e de
controle pneumáticos e electrónicos – equipamentos que continuam a
aumentar persistentemente em quantidade e em complexidade técnica.
No campo dos pequenos sistemas de controle
limitado manteve-se a preferência pela técnica do controle pneumático
com transmissão analógica das informações, mas, mesmo assim,
introduziram-se também numerosos aparelhos electrónicos (alguns de
técnica bastante avançada) quando a variável medida ou o próprio
processo de medição conduzem naturalmente a esse tipo de equipamento e
também no caso de aparelhos laboratoriais (padrões ou ensaiadores da
Secção de Instrumentação e novos aparelhos de medida do laboratório).
Introduziram-se novos sensores de consistência em linha de muito maior
eficácia de medida e resolvendo, até certo ponto, um velho problema de
regulação específico da indústria de pasta e papel (referimo-nos ao
sensor do tipo «lâmina de cimitarra»), medidores magnéticos de caudal,
medidores de condutividade, medidores de pequenos potenciais
electroquímicos com aplicação em aparelhos de análise e controle químico
contínuo (casos do pH e do potencial redox), aparelhagem ultra-sónica de
alarme e de medição de espessuras, aparelhagem radioactiva de alarme de
nível, sensores de proximidade, aparelhos de raios X para exame de
soldaduras, etc. Surgiram os aparelhos miniatura com circuitos
pneumáticos impressos e colocação rápida por encavilhamento, quer das
ligações eléctricas, quer das pneumáticas, os quais se destinam a
resolver o problema do espaço nos painéis. Com efeito, à medida que o
número de aparelhos necessários aumenta (e esse número aumentou
muitíssimo nos últimos anos) os painéis de controle que albergassem
controladores e registadores clássicos tornavam-se impraticáveis dado o
seu enorme tamanho. O problema foi resolvido com os novos modelos do
tipo miniatura nos quais se introduziram os últimos aperfeiçoamentos da
técnica pneumática analógica e que, além de oferecerem inegáveis
facilidades de montagem, de manipulação e de conservação
(encavilhamento, gráfico de rolo, construção modular, etc.), ocupam um
espaço muito menor no painel (embora aumente, mas isso pouca importância
tem, o espaço em profundidade).
/ 35
/
Todos estes sistemas continuam, contudo,
analógicos. Sabemos que, no campo da fluídica, nomeadamente da
pneumática, a tecnologia moderna criou também circuitos digitais, de
certo modo funcionalmente semelhantes aos electrónicos ou de tipos
homólogos a estes, mas nunca os adoptámos na fábrica de Cacia devido aos
seus inconvenientes quando comparados aos circuitos idênticos de tipo
electrónico. Cuidamos que, neste campo, a técnica do futuro aponta para
os grandes sistemas globais e integrados, totalmente automáticos e
comandados por computadores programáveis individuais ou centrais. E aí a
tecnologia da electrónica tem completo e inatacável predomínio, embora
nas zonas periféricas possa aparecer ainda controle fluídico do tipo
analógico, umas vezes por certas vantagens técnicas excepcionais e
pontuais, outras devido ao aproveitamento de material existente (neste
último caso com os problemas resultantes da adaptação de equipamentos
antigos às novas condições de controle avançado adoptadas). Não se
encontra, porém, o nosso país em condições sócio-económicas (e até
culturais, diga-se de passagem...) que, para já, justifiquem a adopção
de tais sistemas ou qualquer opção tecnológica de vanguarda e, por isso,
limitamo-nos aos aperfeiçoamentos pontuais, às consequências da evolução
da técnica do processo sobre o número e os tipos de Iacetes de controle
usados, e ao aumento quantitativo derivado de novos equipamentos de
processo instalados, sempre dentro dos conceitos dos modelos de controle
«clássicos».
Contudo, já não se passa bem a mesma coisa
quando se trata de grandes equipamentos tradicionalmente de comando
global (como a máquina de papel atrás referida) ou em que as condições
de operação impõem um certo grau de automatismo do tipo comutação (a
qual pode ser electromecânica, electrónica ou mista). Nestes casos, a
tecnologia electrónica oferece-nos consideráveis aperfeiçoamentos
imediatamente aplicáveis e que não devemos (e, até certo ponto, nem
podemos) desprezar. É efectivamente o que acontece nas instalações
fabris de Cacia com as duas novas máquinas de tiragem de pasta seca, com
os novos lavadores e difusores de pasta, com uma nova máquina de canelar
que veio, entretanto, substituir a antiga, com várias máquinas novas,
bastante automatizadas, que se instalaram na Fábrica de Embalagens de
Papel, etc.
Evidentemente que não dispomos aqui de
espaço que nos permita referir todos estes casos com um mínimo de
considerações e de dados técnicos. Contudo, vamos tratar muito
rapidamente de um deles e dos mais importantes: o que se refere, dum
modo geral, à electrónica de potência.
Como já tivemos ocasião de dizer, no
accionamento de grandes máquinas multi-seccionais com regulação rigorosa
da velocidade, convém adoptar o motor de corrente contínua, o que impõe
a conversão de corrente alternada para corrente contínua. E, se
possível, essa conversão deverá ser controlada. Na Máquina de Papel, por
exemplo, isso era conseguido através de grupos de geradores e motores e
estava aí, precisamente, uma das grandes fontes de aborrecimentos, de
avarias e de despesas quer de primeiro estabelecimento, quer de
conservação e substituição. É esse um dos grandes males de que padecem
os equipamentos clássicos do tipo considerado. Ora bem: esse problema
foi resolvido pela «electrónica de potência», ou melhor, pela aplicação
da técnica dos semicondutores ao campo da manipulação de grandes
potências eléctricas. Assim, a electrónica invadiu, directamente e com
enormes vantagens, a esfera daquilo a que, nas nossas faculdades de
engenharia, há alguns anos, se chamava «técnica das correntes fortes».
A electrónica de potência compreende a
ligação, desligação, controle e transformação da energia eléctrica
quando se utilize para isso válvulas conversoras, bem como os
correspondentes dispositivos de comando, controle e regulação. No
conceito de válvulas conversoras cabem não apenas as válvulas de vácuo e
as válvulas de descarga, mas também as válvulas de semicondutores, isto
é, rectificadores oximetálicos, de selénio e de silício, transistores e
tiristores.
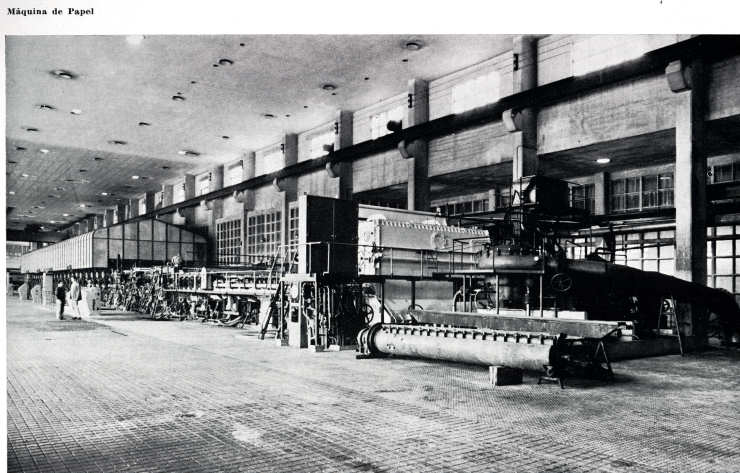
Distingue-se normalmente a parte de potência
e a parte de comando e regulação. Contudo, tanto numa como na outra
empregam-se actualmente componentes básicos de material semicondutor
monocristalino, portanto com exclusão dos semicondutores policristalinos
(rectificadores oximetálicos e rectificadores de selénio). Por isso, na
parte de potência
/ 36
/ surgem-nos díodos
semicondutores, tiristores (sob as suas formas de diacs, triacs e RCS ou
rectificadores controlados de silício) e transístores de potência; na
parte de comando e de regulação, díodos, transístores e os moderníssimos
circuitos integrados. Com uma aplicação de componentes de tipo igual e
normalizado consegue-se uma construção compacta, a maior parte das vezes
modular, de grupos construtivos, com predomínio, sempre que possível, de
circuitos impressos e encavilháveis, até nas próprias instalações de
electrónica de potência, com benéficas consequências no que respeita à
fiabilidade do equipamento.
A electrónica de potência desenvolveu-se,
portanto, a partir da técnica de conversão com válvulas. Semelhante
prática remonta aos anos trinta, pois já nessa altura havia em serviço
um grande número de instalações conversoras com válvulas de vapor de
mercúrio, tanto sob a forma de rectificadores não controlados como
controlados, com potências que iam até à beira dos megawatts.
Inicialmente tinham surgido os conversores mais simples, isto é,
rectificadores não controlados desenvolvidos no princípio do século,
para carga de baterias com redes de corrente monofásica ou trifásica, a
partir dos primeiros rectificadores de vapor de mercúrio construídos, em
1902, por P. Cooper-Hewit. Com o desenvolvimento tecnológico, surgiram
outros campos de aplicação como, por exemplo, a alimentação de
consumidores de corrente contínua de potência média através de
subestações rectificadoras e redes urbanas de corrente contínua, além do
serviço ferroviário com o mesmo tipo decorrente e da electrólise.
As válvulas de vapor de mercúrio dominam
intensidades de 1000 A para tensões da ordem de alguns kV.
Em 1930, entraram em serviço os primeiros
rectificadores de semicondutores, aplicáveis, contudo, a uma faixa de
Potências baixa. Primeiro apareceram os rectificadores oximetálicos e,
pouco depois, os de selénio, cuja base é material semicondutor
tetracristalino. Estes últimos têm-se aperfeiçoado, mantendo ainda
actualmente muitos campos de aplicação como pequenos rectificadores (por
exemplo, rectificadores de alta tensão em aparelhos de televisão).
Nos anos cinquenta, conseguiram-se
desenvolver os primeiros transístores (mas não de potência) e díodos
semicondutores de material monocristalino, primeiro como díodos de
germânio e, alguns anos depois, como díodos de silício, nos quais se
podem alcançar já tensões elevadas. O primeiro transístor foi criado no
campo das telecomunicações pelos laboratórios Bell, nos Estados Unidos,
e, pouco depois, pelo Centro de Investigação Científica dos C T. T.
franceses, em 1948.
Em 1958, a General Electric, nos Estados
Unidos, desenvolvia os primeiros tiristores sob a forma de redificadores
controláveis de silício. Estes novos tipos de semicondutores de potência
controláveis desempenhariam, na técnica da energia eléctrica, durante os
anos sessenta, um papel comparável ao dos transístores nas
telecomunicações, um decénio antes.
No começo dos anos sessenta, os trabalhos de
investigação conduziram a um aperfeiçoamento constante dos componentes
semicondutores e da correspondente técnica de circuitos, o que originou
um desenvolvimento rápido e uma ampliação espectacular dos conversores
clássicos. Ao lado dos circuitos com válvulas de vapor de mercúrio,
tecnicamente perfeitas, conseguiram-se atingir novos tipos de circuitos
e novas aplicações. Estes factos foram favorecidos por dois factores:
pela melhoria das características eléctricas dos semicondutores de
potência, que apresentam consideráveis vantagens relativamente às
válvulas de vapor de mercúrio, sobretudo no que diz respeito à baixa
tensão de disparo e ausência de reacendimento, e muito especialmente
ainda no que se refere ao comportamento dinâmico durante a ligação e
desligação, bem como pelos progressos registados no campo dos
componentes utilizáveis na parte descontrole e regulação, o que permite,
além do mais, a realização de funções complexas de controle e regulação.
A fase presente caracteriza-se pela cada vez maior introdução de
circuitos integrados na parte de controle e regulação.
Pode dizer-se, sem qualquer dúvida, que a
meio da década de sessenta o conceito de técnica de conversão eléctrica
se ampliou definitivamente para a electrónica de potência. Não admira,
portanto, que os novos e mais actualizados equipamentos instalados no
complexo fabril de Cacia se baseiem na aplicação da tecnologia dos
semicondutores, nomeadamente nos tiristores, transístores e circuitos
integrados em suas variadas versões. Se a isto acrescentarmos o rápido
desenvolvimento e aplicação à escala industrial de circuitos lógicos e
de computação, ficaremos com uma pequena ideia da importância cada vez
maior que a electrónica está a assumir entre nós.
Cacia, 5 de Maio de 1978
F. GONÇALVES LAVRADOR
___________________________________________________________________________
* Eng.º Electrotécnico, Chefe dos Serviços de
Conservação de Instrumentos do Centro CACIA
|