1 - Considerações gerais
As instalações fabris da Companhia
Portuguesa de Celulose ocupam uma superfície de terreno de forma
triangular, com uma área de cerca de 400 000 m2, no lugar
da Marinha Baixa, em Cacia, limitada pelo Rio Vouga, pela estrada
nacional Aveiro-Porto e pela linha férrea Lisboa-Porto.
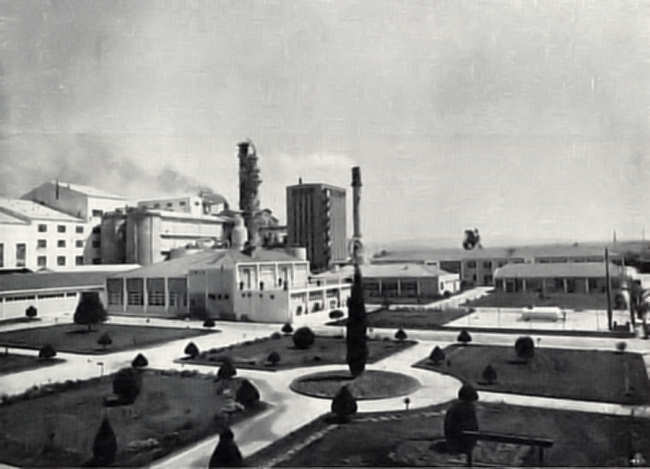
Vista Exterior - lado Sul
A proximidade do Rio Vouga, que
fornece a água necessária para o fabrico, e a da via-férrea e da
estrada nacional, que permitem um fácil aprovisionamento de
matérias-primas e o escoamento dos produtos fabricados, tornam
previlegiada a localização das instalações fabris.
Entrou em laboração no 2.º semestre
de 1953, tendo, então, uma capacidade de produção de 114 t/dia de
pasta de madeira, 100 t/dia de papel e 50 t/dia de cartão canelado.
Essas capacidades de produção são hoje de, respectivamente, 500
t/dia de pasta, 150 t/dia de papel e 80 t/dia de cartão canelado.
Faz-se notar que as capacidades de
produção de cartão canelado se referem a períodos de 14 horas úteis
de trabalho.
Parte da pasta produzida é
branqueada, tendo as
/ 30 / capacidades de branqueio, no
período referido, passado de 100 para 350 t/dia.
Fabrica ainda, a Companhia
Portuguesa de Celulose, sacos de papel e fita gomada, sendo a
produção de, respectivamente, 12 t e 1 t em cada período de 8 horas.
Para além dos aumentos de produção
acabados de referir, também a qualidade dos produtos fabricados
atingiu tal nível, que não há dificuldade em exportar todas as
pastas e papéis produzidos que não são absorvidos em consumo interno
ou pelo mercado nacional.
2 - Fabrico
Todas as matérias-primas naturais
utilizadas no fabrico de papel têm a característica comum de serem
constituídas por fibras celulósicas, ligadas umas às outras por uma
substância termoplástica, a lignina, que confere ao vegetal a sua
rigidez.
Os diversos tratamentos papeleiros
têm por fim:
– dissociar os aglomerados
celulósicos ligados pela lignina, individualizando as fibras.
– aumentar a superfície das fibras
assim libertadas e promover a sua associação de tal modo que formem
uma folha.
A primeira finalidade atinge-se
através dos processos de fabricação de pasta, e a segunda nas
fábricas de papel.
2.1 - Fabrico de pasta
A dissociação dos aglomerados de
fibra pode conseguir-se por meios meramente mecânicos, dando lugar à
formação da chamada pasta mecânica, utilizada no fabrico de cartões
e papéis que não exigem elevada resistência (papel de jornal, por
exemplo); por meios em que a energia mecânica entra numa percentagem
muito baixa, e em que se recorre quase exclusivamente à energia
química, produzindo-se as chamadas pastas químicas; e, finalmente,
por meios que utilizam tanto a energia mecânica como a química, em
quantidades apreciáveis, de que resultam pastas designadas por
semi-químicas.
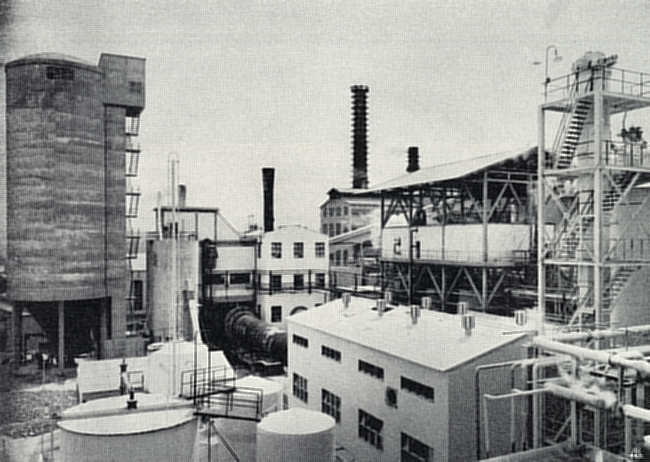
Fornos de Cal e Centrifugação
Presentemente, em Cacia, fabricam-se
exclusivamente pastas químicas pelo processo ao sulfato que produz
pastas de grande resistência, as pastas «kraft» (em alemão, kraft
significa força).
O fabrico de pasta envolve uma série
de operações que, resumidamente, podem esquematizar-se do modo
seguinte:
1) Preparação da madeira
2) Cozimento
3) Lavagem e depuração
4) Branqueamento
5) Tiragem da pasta
Subsidiariamente há ainda a
considerar:
6) Preparação e recuperação da
lexívia
7) Aproveitamento dos produtos
resinosos
A madeira de eucalipto ou de pinho,
que é recebida em toros de 1 a 2 m de comprimento e com diâmetro
entre 6 e 30 cm, é levada a uma estação de descasque donde, já
limpa, segue para os destroçadores. As aparas produzidas são
divididas e classificadas por um crivo oscilante. Aquelas que têm
dimensões apropriadas seguem para o fabrico; as demasiado grandes
voltam aos destroçadores.
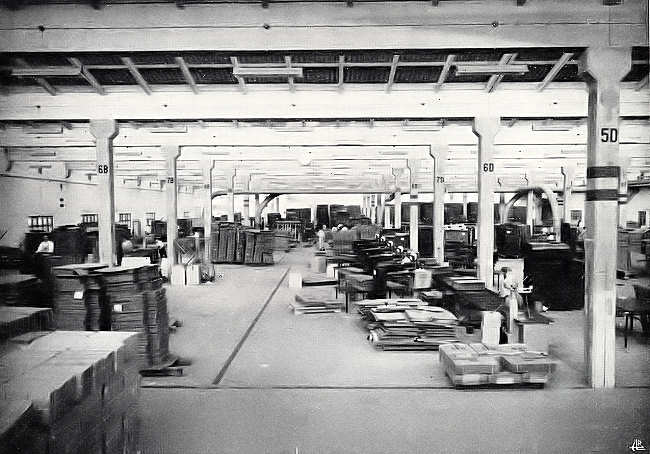
Fabrico de caixas
Para além da madeira em toros,
utilizam-se também desperdícios de serração, que são reduzidos a
aparas numa instalação própria, idêntica à já referida.
Assim preparada, a madeira é então
cozida. O cozimento constitui a principal operação de fabrico e o
seu fundamento químico assenta na acção sobre a madeira, de uma
solução, onde predomina a soda cáustica e o sulfato de sódio (Iixívia
branca).
O cozimento é feito em duas linhas
de fabrico, sendo uma constituída por 4 digestores descontínuos de
85 m3 cada, e a outra, mais recente, por um digestor
contínuo com lavagem incorporada, para uma capacidade nominal de 300
t/dia.
O cozimento, sob pressão, leva cerca
de 4 horas e o aquecimento por meio de vapor é feito por via
indirecta.
Após a cozedura, o conteúdo dos
digestores é descarregado para tanques de maior volume, passando as
aparas de uma pressão da ordem dos 8 kg/cm2 para a
pressão atmosférica, o que provoca o seu desfibramento.
O vapor libertado nas descargas vai
a um condensador de superfície, sendo o seu calor aproveitado para
aquecer água. Também a terebentina da madeira, arrastada por esse
vapor, é recuperada por condensação.
Dos tanques de descompressão a pasta
é bombada para um sistema de lavadores, passando no seu trajecto
/ 31 /
por crivos especiais que retiram os nós da madeira e as aparas não
cozidas.
A classificação final da pasta é
feita em crivos e depuradores centrífugos.
A lexívia separada na operação de
lavagem, que é feita em circuito fechado e contra-corrente, é
enviada a um conjunto de evaporadores, onde a sua concentração é
elevada até cerca de 50% de sólidos, sendo depois queimada em
caldeiras especiais (caldeiras de recuperação) a que voltaremos a
referir-nos.
Para certos casos, é necessário
submeter a pasta a um branqueio tendente a destruir as impurezas que
acompanham a celulose, dando-lhe uma cor castanha.
Existem em Cacia duas instalações de
branqueio de pastas, utilizando na primeira, a mais antiga, cloro,
soda cáustica e hipoclorito de cálcio, e na segunda, cloro, soda
cáustica e dióxido de cloro, e ainda hipoclorito de cálcio em alguns
casos.
A introdução de dióxido de cloro
como agente de branqueio permite fabricar pastas com muito elevado
grau de brancura, mantendo as suas características de resistência a
bom nível.
Quer a pasta branca, quer a pasta
crua (assim é designada a pasta não branqueada) podem ser enviadas
em suspensão para a instalação de fabrico de papel, ou secas,
cortadas em folhas e enfardadas.
As pastas cruas não enviadas para a
fábrica de papel são prensadas até ficarem com 95% de humidade,
cortadas em folhas e enfardadas, e enviadas depois para um local de
recolha, sendo todas estas operações altamente automatizadas.
As pastas branqueadas, antes de
sofrerem as operações referidas para as pastas cruas, são novamente
depuradas e submetidas, após a prensagem, a um processo de
aquecimento, que permite tirá-Ias apenas com cerca de 10% de
humidade.
Quando nos referimos à operação da
lavagem de pasta, escrevemos que a lixívia separada era concentrada
e queimada em caldeiras de recuperação. A esta lixívia dá-se o nome
de lixívia negra e não é senão a lixívia branca utilizada no
cozimento, depois de ter dissolvido os elementos não celulósicos da
madeira. A matéria orgânica dissolvida é utilizada como combustível
nas caldeiras de recuperação, produzindo quantidade muito apreciável
de vapor, e as substâncias inorgânicas, que fundem, caem no fundo da
fornalha e escorrem para um tanque, onde são diluídas.
Antes de se proceder à queima da
lixívia negra, adiciona-se-Ihe sulfato de sódio em pó (daí o nome do
processo – processo ao sulfato –), para assim compensar as perdas em
sulfureto de sódio que sempre se verificam.
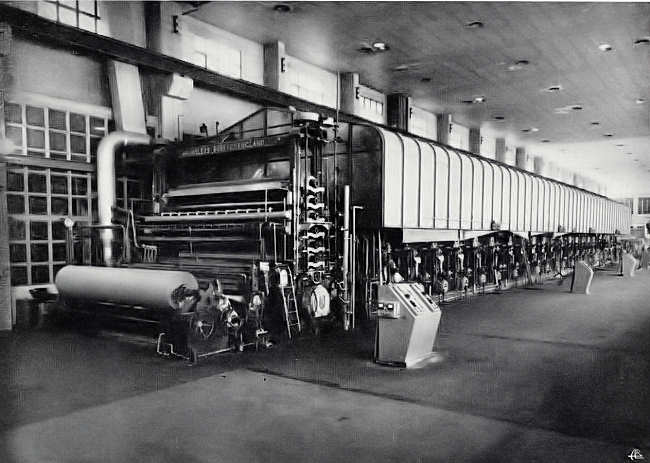
Máquinas de Papel
/ 32 /
A solução de cinzas fundidas, a que se dá o nome de lixívia verde, é
essencialmente constituída por carbonato de sódio e sulfureto de
Sódio.
A composição da lixívia verde é
ainda diferente da da lixívia branca utilizada no fabrico, em cuja
composição, como dissemos, entra fundamentalmente a soda cáustica e
o sulfureto de sódio. Torna-se necessário, portanto, transformar o
carbonato de sódio da lixívia verde em soda cáustica, o que se
consegue pela adição de cal apagada.
Para produzir cal necessária existem
em Cacia duas instalações de caustificação, constituídas por fornos
de cal rotativos, extintores de cal, clarificadores, lavadores,
tanques de armazenamento, etc.
Quando se faz a adição de cal
apagada à lixívia verde, forma-se soda cáustica, como dissemos, e
precipita carbonato de cálcio. Estas lamas de carbonato de cálcio
são recuperadas e, após lavagem, introduzidas no forno de cal
juntamente com algum calcáreo britado, destinado a compensar perdas
que sempre se verificam, sendo aí novamente transformadas em óxido
de cálcio.
A água da lavagem das lamas do
carbonato de cálcio é utilizada na diluição das cinzas fundidas das
caldeiras de recuperação.
Para além da recuperação acabada de
referir, faz-se ainda um aproveitamento de produtos resinosos. A
espuma da lixívia negra é essencialmente um sabão de resina. Tratada
pelo ácido sulfúrico, dá origem a uma mistura de ácidos resínicos e
ácidos gordos, o «tall-oil», utilizável em certas indústrias, como
por exemplo as de vernizes, plásticos, etc.
2.2 - Fabrico de papel
A fábrica de papel de Cacia, que
produz principalmente papéis para cartão canelado, sacos e saquetas
e ainda outros papéis de embalagem, compreende 4 sectores
diferenciados, a saber:
a) Preparação de pastas
b) Máquina de papel
c) Acabamento
d) Armazém
A pasta, quando recebida em fardos,
tem de ser desfibrada para se transformar numa suspensão em que as
fibras estejam, tanto quanto possível, individualizadas.
Esta operação é levada a efeito em
dois desfibradores, cuja capacidade pode ir até cerca de 10 t/hora.
Uma vez desfibrada, a pasta é
tratada em aparelhos designados por despastilhadores, destinados a
completar o processo de desfibração, e daí vai aos refinadores, que
tendem a aumentar a superfície das fibras, transformando cada fibra
num feixe de fibrilas que,
/ 33 /
absorvendo água, aumentam de volume, tornando-se flexíveis e
gelatinizando-se parcialmente. Também os refinadores são utilizados
para cortar as fibras, quando estas são demasiadamente longas.
A pasta assim tratada é depois
depurada em crivos rotativos e em depuradores centrífugos, seguindo
daí para a máquina de papel, após a adição de quantidade
considerável de água, que é retirada durante o processo de fabrico
de papel.
Essa suspensão muito diluída entra
numa caixa em que se mantém uma altura de líquido variável com a
velocidade que se pratica e que tem uma saída inferior de abertura
regulável, que permite que se deposite sobre uma tela metálica
sem-fim e a toda a sua largura, um caudal constante.
Essa tela sem-fim, de malha aberta,
que na máquina de Cacia tem uma largura de cerca de 4,70 m e um
comprimento de 30 m, é mantida em movimento por um cilindro
aspirante e apoiada sobre rolos cobertos de borracha e caixas
aspirantes.
A água, por gravidade e pela
aspiração provocada pelos rolos, caixas aspirantes e pelo referido
cilindro aspirante, vai-se escoando à medida que a tela se vai
deslocando.
Atingido o extremo da tela metálica,
a folha de papel já formada, embora ainda com uma elevada
percentagem de água, é depositada sucessivamente sobre três feltros
de lã, passada através de três prensas e posta depois em contacto
com 41 cilindros secadores de 1,5 cm de diâmetro, aquecidos com
vapor.
Passa finalmente através de uma
calandra e é enrolada em volta de um veio metálico.
A máquina de papel de Cacia, embora
montada há já 15 anos, é ainda a máquina de maior capacidade de
produção existente no nosso país, podendo produzir papel com uma
largura de 4,40 cm, à velocidade de 440 m/min.
Uma vez fabricado, o papel segue
para a secção de acabamento, onde é cortado em bobines com as
medidas desejadas que, embaladas ou não, seguem para armazém. Daí,
ou é expedido em bobines ou segue para uma das duas cortadoras
existentes, para ser cortado em folhas e enresmado ou enfardado.
2.3 - Fabrico de cartão canelado
O cartão canelado, material básico
para o fabrico de caixas para embalagem, é fabricado em Cacia numa
máquina com 2,20 m de largura, capaz de atingir uma velocidade de
200 m/min.
Uma vez formada, a prancha vai a um
conjunto de cinco máquinas ranhuradoras – vincadoras – impressoras,
de características e possibilidades diferentes, sendo possível
imprimir a três cores.
Dessas cinco máquinas, a mais
aperfeiçoada
/ 34 / permite a colagem da patilha das
caixas e é capaz de uma produção de 18000 caixas/hora.
A fixação da patilha nas caixas não
fabricadas nesta máquina é feita por agrafagem.
3 - Produção de vapor e energia
O vapor, produzido a uma pressão de
63 kg/cm3 e a 4250 C, é gerado, como já referimos, por
duas caldeiras de recuperação, que são capazes de uma vaporização de
75 t/h, e por duas caldeiras a «fuel-oil», que podem produzir 70
t/h. Uma terceira caldeira para 100 t/h será montada brevemente.
O consumo anual de fuel-oil anda
pelas 55000 toneladas.
A energia eléctrica é gerada por
dois grupos turbo-gerados, com uma potência de 13125 kW, um de
condensação com duas extracções e outro de contrapressão. Um
terceiro grupo de 22 700 kW, já adquirido, será montado dentro de
pouco tempo.
4 - Água
A água para o fabrico é bombada do
rio Vouga, consumindo-se cerca de 1000 I/s na plena produção da
Fábrica.
5 - Alguns dados com interesse
Para se avaliar do grau de
importância desta unidade fabril no distrito e na própria Economia
Nacional, anotamos alguns números que nos parecem elucidativos:
Pessoal que presta serviço na
Empresa
– cerca de 1 500 trabalhadores
Ordenados e salários
– cerca de 60000 contos/ano (inclui
cerca de 9000 contos de encargos sociais)
Encargos com a política social da
Empresa
– cerca de 4300 contos/ano
Imposto de Comércio e indústria
(Câmara de Aveiro)
– cerca de 4000 contos/ano
Pasta exportada pelo porto de
Aveiro no primeiro semestre de 1969
– cerca de 32 000 toneladas
N.º de refeições (almoços e
jantares) servidos na Cantina da Empresa em 1968
– cerca de 273 000
|